Keep your workspace safe & compliant
Your One Stop Welding Shop
Superior Range
Sell/Hire/Service/Repair
Expert Advice
WELDING FUME MANAGEMENT
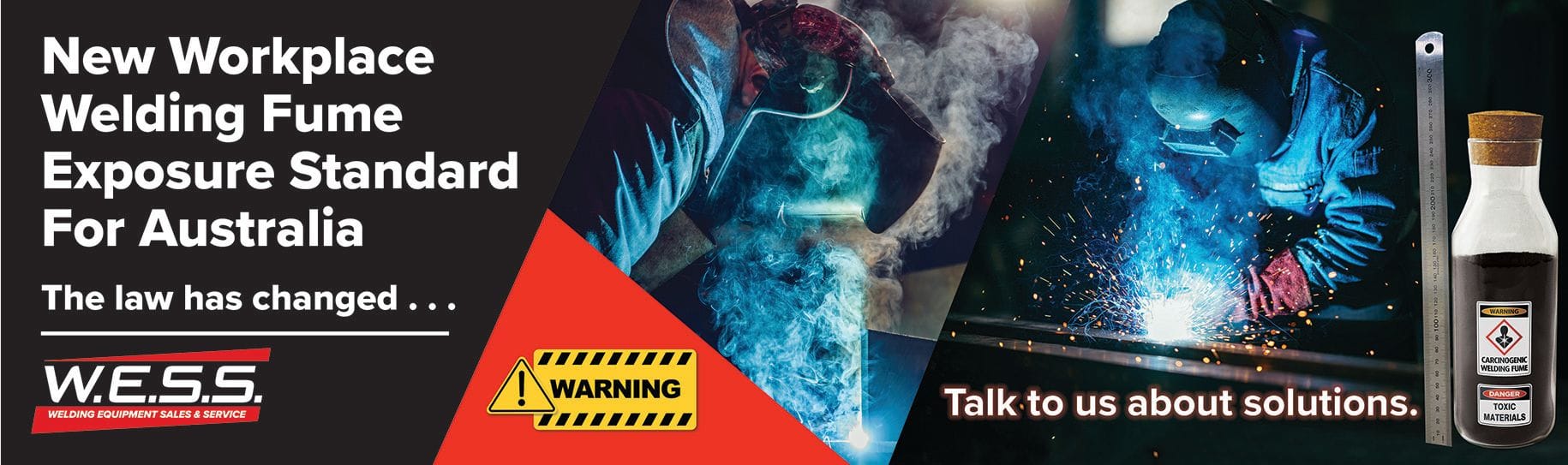
The WESS Team have you covered with many years of experience and knowledge of both local and global markets and industry trends including the latest related to welding fume and todays accepted best practices in Welding Fume Management. Our experienced team will provide the expert advice for all the latest requirements and best practices in Welding Fume Management.
WHERE TO START:
ENSURE YOUR WORKSHOP MEETS THE LATEST WELDING SAFETY STANDARDS
STEP 1: PARTNER WITH US TO ASSESS YOUR SITUATION.
In collaboration with HSE Australia, we'll conduct a thorough, independent assessment. All collected data is analysed in a lab and results will be provided to you in a detailed report.
STEP 2: IMPLEMENT SOLUTIONS.
Based on your assessment, WESS will work closely with you to implement the most effective solutions tailored for your workshop's specific needs.
Keeping your workers safe is our top priority and we're here to support you with expert advice and effective solutions. Contact us today to start improving your workspace safety.
Foreground
In 2017 the IARC (an agency of the World Health Organisation) announced a ruling in relation to welding fume being reclassified from Group 2B Possibly Carcinogenic to Humans to Group 1 Carcinogenic to Humans.
Responsibilities of Employers & Employees
Federal and state regulations set out the responsibilities of manufacturers, employers and employees. With respect to welding and allied processes the following requirements apply.
Employers: Persons conducting business or undertakings must:
- Develop and subsequently maintain a register of all hazardous chemicals used or produced in the workplace. This may include consumables, welding fume or any other hazardous chemical in the workplace
- Maintain a collection of SDS also known as MSDS (material Safety data Sheets) as part of the register. This register must be available for reference by all employees
- Ensure a suitable and sufficient assessment is made of the risk to health created by welding fume or other hazardous substances
- Revise the assessment at least every 5 years or if workplace conditions change significantly
- Provide training to all employees with the potential for exposure to welding fume
- Keep records of training and assessment. Reports must be available to employees to whom the assessments relate
- Provide health monitoring for employees assessed as being exposed to a significant health risk in the course of their employment duties
- Undertake monitoring where the need is indicated in the assessment
- Ensure that exposure of employees to hazardous chemicals is prevented or adequately controlled to minimise risk to health. Exposure must not exceed the relevant exposure standards
- Ensure that engineering controls and safe work practices are effectively maintained
Employees are required to:
- Cooperate with the employer to ensure that activities within the workplace comply with the statutory requirements
- Report promptly to supervisors/managers any matter that might diminish the employer's ability to achieve compliance
Recommendations
In compliance with National and State WHS Regulations, conduct a risk assessment to ensure that the welder and people working nearby, are protected from exposure to fume from welding and welding-related processes (including thermal cutting, gouging etc.). The following actions should be considered in the risk assessment:
1. Where practicable, remove the welder from the source of the fume by mechanising or automating the welding process.
2. Arrange the work piece so that the welder's head is not in the plume.
NOTES: (i) Unless welding in the horizontal (PC or 2G), overhead (PD, PE, 4F, 4G) or vertical (PF, PG, 3F, 3G) position, the welder's head is likely to be positioned within the plume, and fume management methods or personal protective equipment (PPE), or a combination of both, may be required. (ii) All welding processes generate fume. The plume may not be visible to the welder or with some processes, the observer.
3. Relying on a light cross-draught in the vicinity of the welder's face to ensure that the fume is either drawn or blown away from the welder's breathing zone can be unreliable. Whilst mechanically assisted ventilation (e.g. a fan) can be utilised, cross draughts sufficient to disperse fume may cause weld quality issues. Other fume management equipment such as fume extractors (e.g. fixed, downdraft or portable) may be required.
4. Utilise personal protective equipment such as respirator masks and air fed helmets (PAPR) if alternative methods of fume control are not reasonably practicable. Care should be taken to ensure that other workers are not exposed to the fume by allowing it to accumulate in areas away from the welding or welding related process.
Specialist advice may also be sought from an Occupational Hygienist e.g. www.aioh.org.au, particularly in the preparation and implementation of the risk assessment, and the verification of the application of the controls.
Further information can be found in Weld Australia TGN-SW01
Today’s Most Accepted Industry Fume Management Solutions
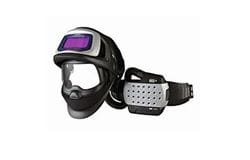
PAPR Systems (Powered Air Purifying Respiratory)
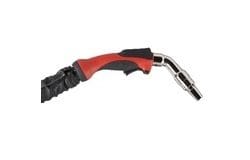
Welding Fume Extraction Guns
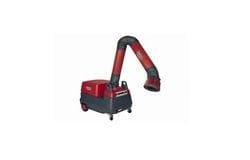
External Fume Extraction Systems
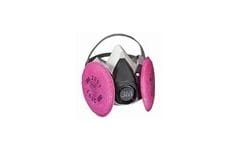
Respiratory Masks

Looking for a job in the Welding Industry?
We want to help. Submit your details here to allow perspective employers to view.
Keep In Touch.
Join our WESS Masters Network. Stay up to date on the latest in welding technologies, new products and special offers. Also find us on your favorite social network.
Help us get better.
Please give us your feedback on our performance. We strive for continuous improvement and want to be the industry benchmark.
Promotion Centre.
Review our current promotions here.
SHOP DETAILS
Wingfield, 5013
South Australia
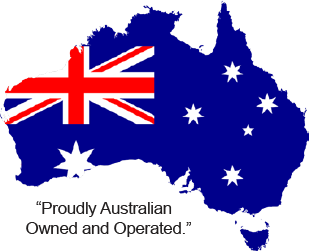